热喷涂涂层样品制备
THERMAL SPRAY COATINGS Sample Preparation
For equipment that operates in harsh or demanding environments, thermal spray coatings offer a secondary layer of protection against environmental conditions and contamination on new parts, or a restorative layer to extend the service life of a worn component. Thermal spraying applies a coating onto a substrate with a range of available materials to improve performance. The type of coating material used may vary based on the needs of a given application, making it essential to choose the correct coating in advance. Making the incorrect choice can lead to premature coating failure, which subsequently leads to failure of the original substrate.
Thermal spray coatings can be applied across large or small surfaces, making them ideal for myriad applications where large equipment or structures need additional protection. For example, the aerospace sector often uses thermal spray coatings to enhance wear resistance, thermal protection, and corrosion in components throughout turbine engines.
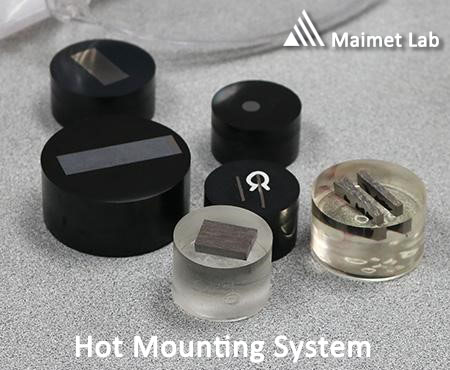
BENEFITS PROVIDED BY THERMAL SPRAY COATINGS
Thermal spray coatings deliver several benefits for manufacturers, including:
· Increased resistance
Thermal coatings can be used to increase resistance to wear, erosion, cavitation, corrosion, abrasion, heat, chemicals, and more.
Additional material characteristics
Certain thermal spray coatings can be used to enhance or apply desired characteristics to a substrate, such as electrical insulation or conductivity, high or low friction, lubricity, sacrificial wear, thermal protection, dimensional restoration, and chemical resistance.
· Increased service life
Thanks to improved resistance to environmental factors, thermal spray coatings may drastically increase the useful life of a part or surface.
· Revitalization
Even if a substrate doesn’t begin its service life with a thermal spray coating application, applying one at a later production or implementation stage can facilitate repair or re-engineering of worn or damaged components.
INDUSTRY APPLICATIONS FOR THERMAL SPRAY COATINGS
Many industries use thermal spray coatings to add enhanced properties to components. Thermal spray coatings are especially useful for parts that must operate under extremely demanding or harsh conditions, specifically those intended for use in the following industries:
AEROSPACE
High-performance aerospace components must tolerate extended service lives while withstanding extreme temperatures, drastic changes in pressure, impact stresses, and exposure to corrosive environmental elements. Because raw materials and finishing methods typically offer insufficient protection for these parts, thermal spraying is often employed to further improve the longevity and resilience of:
Equipment used in the fossil fuel and renewable energy sectors must tolerate extreme temperatures, varying pressures, and environmental exposure. As such, the power and energy sector uses thermal spray coating to improve the properties of a wide range of components, such as:
Thermal spray coatings can also be useful in the petrochemical industry, where exposure to high pressures and corrosive chemicals can severely impact the service life of equipment. Coatings are used to increase resistances on a variety of components in this sector, including:
Maimet Test Labs offers a wide range of testing services to provide a thorough analysis of thermal spray coatings. Thermal spray coatings can be tested in a variety of ways to ensure fitness for a given application or determine causes for failure. These methods include:
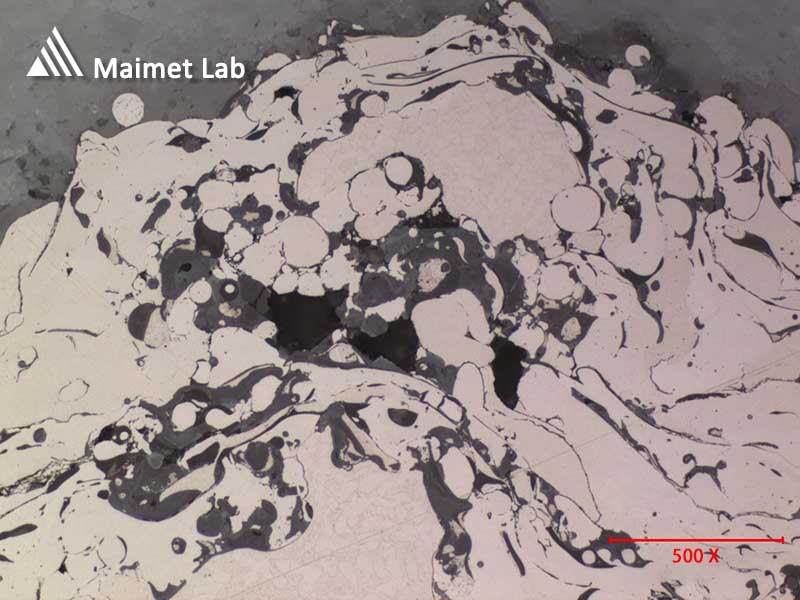
For equipment that operates in harsh or demanding environments, thermal spray coatings offer a secondary layer of protection against environmental conditions and contamination on new parts, or a restorative layer to extend the service life of a worn component. Thermal spraying applies a coating onto a substrate with a range of available materials to improve performance. The type of coating material used may vary based on the needs of a given application, making it essential to choose the correct coating in advance. Making the incorrect choice can lead to premature coating failure, which subsequently leads to failure of the original substrate.
Thermal spray coatings can be applied across large or small surfaces, making them ideal for myriad applications where large equipment or structures need additional protection. For example, the aerospace sector often uses thermal spray coatings to enhance wear resistance, thermal protection, and corrosion in components throughout turbine engines.
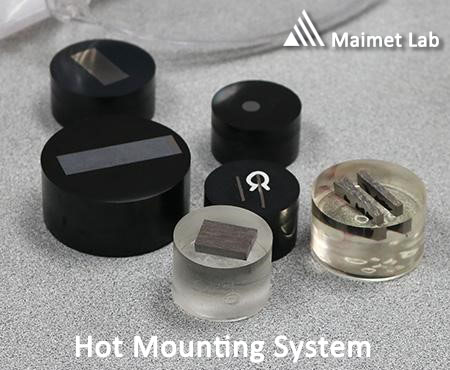
BENEFITS PROVIDED BY THERMAL SPRAY COATINGS
Thermal spray coatings deliver several benefits for manufacturers, including:
· Increased resistance
Thermal coatings can be used to increase resistance to wear, erosion, cavitation, corrosion, abrasion, heat, chemicals, and more.
Additional material characteristics
Certain thermal spray coatings can be used to enhance or apply desired characteristics to a substrate, such as electrical insulation or conductivity, high or low friction, lubricity, sacrificial wear, thermal protection, dimensional restoration, and chemical resistance.
· Increased service life
Thanks to improved resistance to environmental factors, thermal spray coatings may drastically increase the useful life of a part or surface.
· Revitalization
Even if a substrate doesn’t begin its service life with a thermal spray coating application, applying one at a later production or implementation stage can facilitate repair or re-engineering of worn or damaged components.
INDUSTRY APPLICATIONS FOR THERMAL SPRAY COATINGS
Many industries use thermal spray coatings to add enhanced properties to components. Thermal spray coatings are especially useful for parts that must operate under extremely demanding or harsh conditions, specifically those intended for use in the following industries:
AEROSPACE
High-performance aerospace components must tolerate extended service lives while withstanding extreme temperatures, drastic changes in pressure, impact stresses, and exposure to corrosive environmental elements. Because raw materials and finishing methods typically offer insufficient protection for these parts, thermal spraying is often employed to further improve the longevity and resilience of:
- Turbine blades
- Flame tubes
- HPT outer stationary seals
- Liners
- Landing gear
- Jet engine components
Equipment used in the fossil fuel and renewable energy sectors must tolerate extreme temperatures, varying pressures, and environmental exposure. As such, the power and energy sector uses thermal spray coating to improve the properties of a wide range of components, such as:
- Power generators
- Gas turbines
- Turbine rotors
- Compressor blades
Thermal spray coatings can also be useful in the petrochemical industry, where exposure to high pressures and corrosive chemicals can severely impact the service life of equipment. Coatings are used to increase resistances on a variety of components in this sector, including:
- Pump impellers
- Pump castings
- Pipes
- Mud pump components
- Gate and ball valves
Maimet Test Labs offers a wide range of testing services to provide a thorough analysis of thermal spray coatings. Thermal spray coatings can be tested in a variety of ways to ensure fitness for a given application or determine causes for failure. These methods include:
- Metallographic analysis
- Microhardness measurements
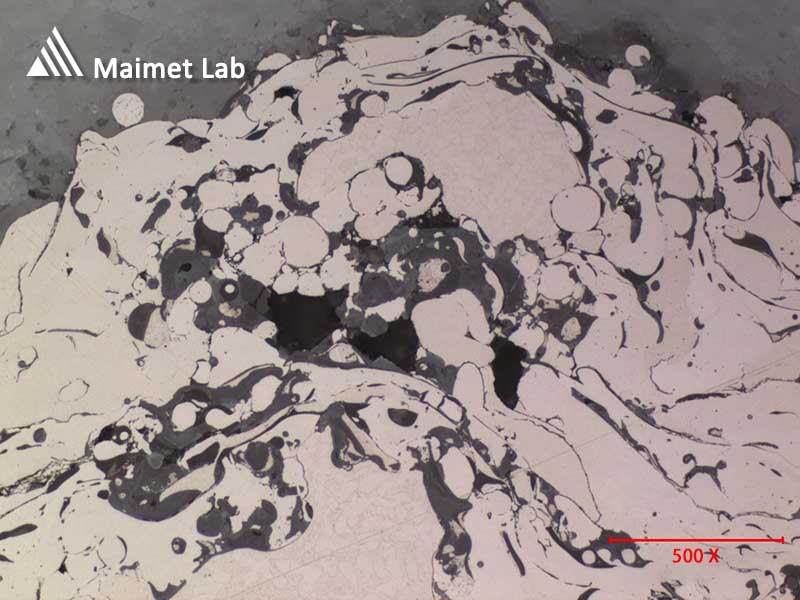
- 上一篇:抱歉,没有了。
- 下一篇:铸铁样品制备 - 曲轴
将您的信息发送给我们:
